Biopharmaceutical Air Frame Filtering: Its Applications
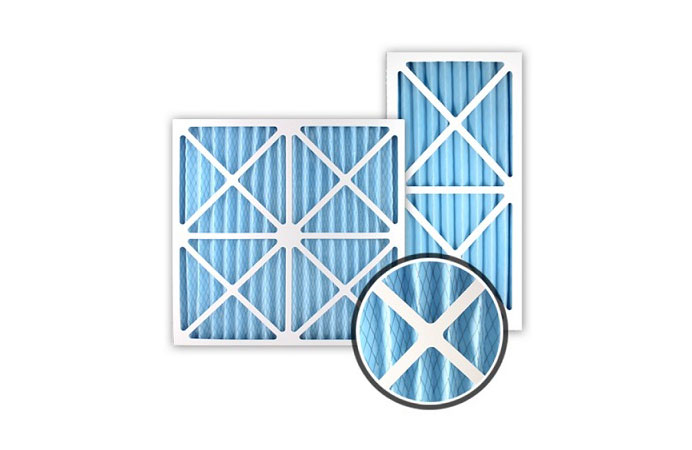
In the realm of biopharmaceutical manufacturing, air quality is paramount. Contamination can lead to product degradation, increased batch failures, and, ultimately, compromised patient safety. Among the various air filtration techniques, the air frame filter, also known as the plate-and-frame filter, holds a prominent position due to its high efficiency and adaptability.
The air frame filter consists of a series of filter plates, typically made of stainless steel or other corrosion-resistant materials, arranged in a frame. These plates are designed with intricate channels and grooves that, when assembled, create a series of filtration chambers. The filter media, often a porous material such as cellulose or synthetic fibers, is placed between these plates, creating a surface area large enough to trap particles effectively.
The working principle of the air frame filter is straightforward yet effective. As air passes through the filter, particles larger than the pore size of the filter media are trapped, while the clean air passes through. The trapped particles accumulate on the filter surface, gradually reducing the filtration efficiency. Regular cleaning or replacement of the filter media is thus necessary to maintain performance.
In biopharmaceutical applications, the air frame filter is often used in cleanrooms, where strict air quality standards must be met. These filters can remove dust, bacteria, and other microorganisms, ensuring a contaminant-free environment for manufacturing processes. Additionally, they can be customized to target specific contaminants, making them highly versatile in different manufacturing scenarios.
The advantages of the air frame filter are numerous. It offers a high filtration efficiency, especially when used in combination with other filtration techniques. Its modular design allows for easy scaling, making it suitable for both small-scale research laboratories and large-scale manufacturing facilities. Moreover, the filter plates can be easily disassembled and cleaned, reducing maintenance costs and downtime.
However, like any other filtration system, the air frame filter has its limitations. It may require frequent cleaning or replacement of the filter media, depending on the contaminant load and the desired filtration efficiency. Additionally, the initial cost of the filter system can be relatively high, especially for large-scale applications.
The air frame filter is a crucial component in biopharmaceutical air filtration. Its high efficiency, scalability, and ease of maintenance make it an ideal choice for ensuring contaminant-free air in manufacturing environments. As the biopharmaceutical industry continues to evolve, the air frame filter will likely play an increasingly important role in maintaining product quality and patient safety.